Methodology
The drilling technique we use is a Rotary Mud System. On larger diameter bores, a top starter casing will be cable tooled into place using a crane. This is to isolate upper ground materials/water from the main bore. The main bore drilling follows and the hole is held open with drilling mud. As the cuttings are pumped from the bore they travel across a shale shaker screen and the cutting material is recorded. This record is referred to as the bore log. When a water bearing aquifer is discovered, a sample of material is taken to determine the slot size of the well screen. Casing is installed down to the aquifer and the screen is lowered inside the casing and locked into place.
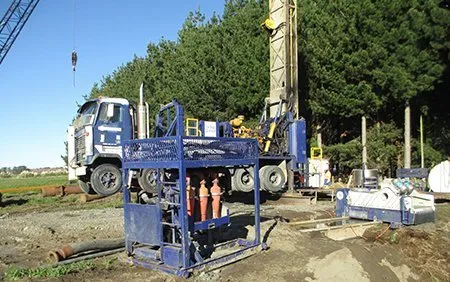
The rotary mud method has several advantages over cable tool drilling.
- Elimination of ground shock waves and impact noises.
- Ability to easily drill ahead of starter casing, without bore collapse, regardless of strata type.
- All drill cuttings are passed over the shaker upon exiting the bore. This allows drilling fluid and cuttings to be recovered separately. (Cable tool cuttings are normally recovered in solution.)
- Cuttings can then be clearly analysed to determine the different geological strata.
- The drilling fluid is recycled through hydro-cyclones and mud tank. This process maximises cutting recovery and minimises drilling fluid requirements for any given bore depth.
- The use of drilling fluid seals the bore during drilling and prevents any cross contamination of aquifers for any uncased area during the drilling operation.
- Drilling fluid density can be adjusted at any time to control the effects of artesian flow when encountered.
- Recycling of the drilling fluid minimises discharge from the site.
Mechanical Seals
Unique Seal Design -We will use a manufactured screw up seal rather than “k” packer seal rubbers. Extensive tests were undertaken with “k” packer and screw up seals when constructing the Wanganui District Council’s town water supply bores.
The results showed that “k” packer seals would only hold 16.5psi of pressure whereas our screw up sets would hold 1000psi.
We have proved in deep bores that most sand intrusion occurs when “k” packer seals are used. The design of a “k” packer seal means the seal rubber is in contact with the casing all the way from the surface to the final screen location. This damages the rubber lips.
Our manufactured screw-up seals have been designed to protect the sealing rubber within the assembly during installation. Considerable development time and money was spent to design our seals.
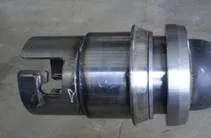
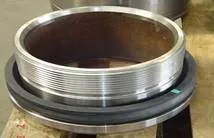
Bore Logs and Your Bore Quote
Wanganui WellDrillers Ltd has built up a comprehensive library of bore logs. These provide a geological profile of the strata that is drilled through when looking for a water bearing aquifer.
With this knowledge, technology and experience, Wanganui WellDrillers can confidently advise the depth at which water might be found.
Depending on a your requirements, we can quote on a 6″ bore for shed supply, a 6″ to 8″ bore for a farm supply or 12″ plus irrigation bores for cropping or dairying operations.
Our quotes are obligation free. We will personally meet with you on site to discuss a quote and where the bore is to be drilled.
WellDrillers Screens
Water occupies the space between sand and gravel in an aquifer. A screen is used to keep the sand and gravel out when pumping the water. During the drilling process, a sample of the aquifer material is retrieved and analysed to determine the size of screen required so that the sand and gravel does not enter the well and damage the pump.
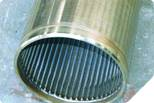